Eurovision Song Contest 2021: audio – lights – rigging
1782 automated fixtures: Ayrton, Robe, Clay Paky, GLP
Control: 16 grandMA3 light, 30 Processing Units
Follow-Me 3D: 64 follow spot fixtures, PSN-motion integration
Robe RoboSpot follow spot system + Motion Cam
6 Capture stations: pre-prog lighting, content, broadcast
2653 Metres of trussing
506 electric chainhoists
220 tons of static load
298 Speaker cabinets: L'Acoustics, Synco
4 DiGiCo Quantum7T Consoles
20 Shure Axient digital quad receivers
4200M of speaker cables
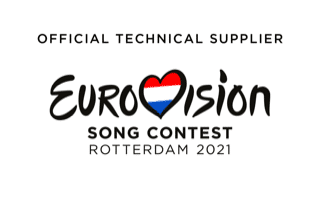
May 25, 2021
Open up!
Duncan Laurence’s win in 2019 brought a lot of wheels in motion, which came to a sudden stop due to COVID. We will always remember how much our industry had to endure, and will always be proud of the way our industry dealt with the immense challenges. Eurovision was one of the events that marked a new beginning, some light at the end of the tunnel and was an honour to work on. Let’s hope that all our event colleagues all over the world can work on their passions as soon as possible. Keep safe!
A tribute to the graveyard shift
Daytime in Ahoy set the stage for delegations, directors, rehearsals, make-up and audience. When the night falls, our graveyard shift wakes up: during loadin, during rehearsal- and showdays and during loadout AHOY is their territory: Maintenance, repairs, checking network and hardware statuses, keeping all components in perfect condition and if needed working in the grid with cherrypickers. Our valuable vampires were also on the spot right after the award ceremony, clearing the stage and floor to make way for the grid to be lowered. As we speak AHOY will be almost empty, and our crew can almost relax and spend some time off..
What a journey..basta!
Congratulations to Italy, and a big thank you to all involved in this wonderful journey.
Our job is not done on saturday. The same amount of skill and dedication that went into the build will be shown during load-out.
The amazing world of TV
The Eurovision Song Contest is primarily a TV show and the amount of technology used to get the show on your screen is amazing, a technology that we are also a part of. One of them is the way that cameras, lighting, video and motion are controlled by one system, resulting in spot-on timing and control. Photos: Nathan Reinds / Ralph Larmann
A little while ago we showed you the previsualisation and preprogramming room in Amsterdam. LD’s and Multicam Director used Capture 3D rendering making it possible to determine camerashots and visuals in advance.
More TV-info via our colleagues at NEP-The Netherlands
Nerd alert part III: Audio specs
Besides the usual challenges in a competition with many different kinds of artists and 200 million viewers on TV, this year COVID forced the audioteam into extra measures that worked out flawlessly.
For all you audiogeeks and gearheads: read the full audio gearlist here
Semifinal 2: in the pocket
Semifinal 2 was one to remember. Now let’s get some sleep and prepare for the finals on saturday…
Nerd alert part II: Lighting specs
Yesterday’s semifinal 1 finally showed the result of all the lighting we installed in Ahoy. Curious about the types and numbers?
But it doesn’t stop there: the whole venue is turned into a stage! Read the full lighting speclist here
Semifinal 1: check!
This is what we have been working on, and what we have been looking forward to. Semifinal 1 is done and dusted. Let the pictures speak for themselves.
Nerd alert: Rigging
For all you gearheads we counted all the rigging equipment we are using in AHOY during ESC. First in, last out; the rigging has the longest residency.
What hangs where? read all about it here!
Matchweek!
We have trained, practiced, prepared and cooperated. let the games begin.
Calm before the storm
Final rehearsals for all artists and crew. We are ready for Matchweek.
Interview with Head of Production
Erwin Rintjema, head of production, makes time for an interview for Dutch TV. Very nice of them to make time for the technical side of this production! (Interview is in Dutch, so grab your dictionaries)
A deskjob Jim, but not as we know it
Desks all around, and the specialists to operate them.
People let your light shine!
To make sure that it will not be Waterloo, preparations have been meticulous. What’s another year when you don’t shine?
Testing 1, 2…
Did you know why soundguys only count to 2 ? At 3 they have to lift something.
Full Focus..again
Meanwhile in the followspot-room, our crew is concentrated on the rehearsals as well. The mix of Robe RoboSpot and follow-me systems gives the Lighting operators total flexibility in the keylight department.
Full Focus
Rehearsals are well on the way and showcrew is fully focused towards the semifinals and the finals. Let’s go!
Every changeover is planned and rehearsed in all details, from wireless to lights, from costumes to backline and props.
Load-in timelapse
Jorrit lousberg made this fabulous timelapse: from first chalk on the floor to a complete stage!
Ready for action
The stunning stage is set for continuous rehearsals. On our way to the liveshows!
Follow them!
In the past heavy followspots had to be manually operated from somewhere back in the venue or hoisted up in the grid. During this production we make use of the newest followspot technology!
Ready for rehearsals
Each delegation gets the opportunity for rehearsals, to create a fair competition. This is also the time for detailing and finetuning camerashots, lighting, audio and video. Here are some stunning views of the stage, shot by Nathan Reinds.
It’s the people that do the job
Cooperation is key in a production like ESC. Working together with other suppliers gives the best result!
Clay Paky Xtylos all around
One of the main moving lights specified by the Lighting Designers is the Clay paky Xtylos with its laser-like beam and precision. Not just for lighting the stage, but also as a very impressive audience and arena effect.
Preprogramming
While AHOY was being transformed into the ESC Arena, Lighting Designer Henk-Jan van Beek and First Multicam Director Marnix Kaart were preprogramming lighting, cameras, motion and video in Amsterdam. We interviewed them about the ins and outs.
Pass the mic!
There is more to wireless this year than distribution to the artist and frequency management: health and safety are top-priority in these COVID times. When entering Ampco Flashlight’s ‘wireless plaza’ a strict and very practical protocol is in place.
The smallest fixture
Sometimes small is better!
Audio: everything under (redundant) control
Ready for rehearsals. On top of the experience and knowledge of the crew all audiosystems have a high level of redundancy and safety.
photos: Nathan Reinds
A lot of lights
The lighting systems are split into multiple main departments. Among them are programming, controls, networking, power and followspots (more about those later!)
photos: Nathan Reinds
Frequency watching
Now that all wireless racks are installed we can start finetuning on all accessories and frequencies. Also measured is any interference from outside the venue.
Weight watching
Through loadcells we can measure the weights on various key points in the grid.
Equipment is beautiful
Some shots, made a week ago, of the ‘ceiling’ above the AHOY venue.
Excerpts from pictures by Nathan Reinds.
A Royal visitor
Ahoy had the honor of welcoming his royal highness King Willem Alexander. Shown around the venue and backstage he (like any visitor) was impressed by the scale and technology of this year’s ESC. Something to be proud of !
Pictures by Nathan Reinds.
Pre-programming studio
While the stage is being built in Rotterdam, rehearsals are already taking place in Amsterdam. These are virtual rehearsals made possible by using sophisticated software. Lights, Video, Motion and Cameras are all integrated virtually so the director can see the results in his actual camerashots. Saves valuable time of the venue and of the performers!
Wireless control room
Aart and his team have set-up and settled. Time for testing, finetuning and connecting the feeds to the audionetwork.
Audio update
Our audiocrew is working on building the infrastructure, including the consoles. Our wireless controlroom is almost operational and ready to start receiving and transmitting!
Measuring..
Fortunately some of our crew were allowed to play outside. Although it wasnt really clear what they were doing.
Building the stage
A lot of people are curious what the stage will actually look like. We won’t tell, you will probably see tomorrow! In the meantime we are working on that same stage. Pictures by Nathan Reinds.
Some professional pictures
Thanks to our crew at production we receive a steady stream of pictures. Besides that the talented Nathan Reinds is also on the spot to capture ESC from beginning to end. Always nice to have him and his camera around. Here are some of his photos from last friday!
Getting our hands dirty
Still on schedule!
Keeping fit
To keep our crew fit, a special gym is provided for necessary exercise.
Audio Techdecks
To drive the audiosystem 4 techdecks have been hoisted to about 20M high.
Patchprinting and sunbathing
The most important part of a lighting system is the people that work on it..
Stuff in flightcases
Someone once asked a roadie if he could tip the waitress. Fortunately she only suffered minor bruises. Ever since our industry started we have been moving stuff around in flightcases. We should start calling them gearcases!
Steadily moving on
The floor is cleared but we still have enough work for our riggers. Trusses above the audience stands, adjustments, checks and assisting other technical parties.
Set building
Now that the ceiling is up, the stage can be built. Our first sprint is done, next one is connecting all systems and build the floorsets for audio and lights.
Pointing at a drawing
A job like this requires a good preparation, coordination and looking at drawings. It’s good to see people working together!
I’m on fiber
With a lot of equipment in the right place it is now time to start connecting it all, while also working on filling the gaps.
Meanwhile at homebase
Business as (un)usual
While colleagues are working in Rotterdam and on other jobs in other places, our warehouse in Utrecht is the place where we keep our stock up to date and clean, anticipating busier times for everyone.
(Our crew wears masks when moving through the building, but can take it off when performing stationary jobs)
Wireless!
Some numbers:
Wireless mics:
20 Shure Axient digital quad receivers
40 Shure ADx2FD handhelds
30 Shure ADx1 beltpacks
100 DPA 4088 headsets
Wireless in-ear:
11 Shure PSM1000 dual transmitters
72 Shure P10R bodypack receivers
Clearing the floor
Just a few days after the first cases were loaded in, the first part of the trusses are already up, loaded with equipment and cabling, also including loudspeaker clusters. This makes the floor available for building the set and stage. For reaching the truss we can use the cherrypickers that are available. Just don’t be afraid of heights..
People
Filling up the truss
All 1782 automated fixtures have been tested in our warehouse, and will be tested again during build-up -before being hoisted up- using our mobile test-rack. In this case a bunch of Robe Spiiders. (And as you of course know spiders are NOT insects, but Arthropods!).
Finally..back to work
Probably just like you, we have been waiting for ages until we could go back to doing what we love: working behind the scenes and helping to make a great show. Coming in when the hall is still cold and empty, leaving when artists and audience have long gone. We don’t mind as long as we can do our thing. We are extremely proud of our ESC team, our colleagues at the office supporting them, and of the colleagues working at other jobs for our variety of special clients. We are also proud of all the companies and leaders from our industry who succeeded in building instead of complaining, making plans and moving forward. We trust to see all of you doing what you love very soon. Even if it means giving up a modeling career, like some of our colleagues..
(tested every 48 hrs!)
Visualisations & first light hanging
In a studio, somewhere in the Netherlands, our equipment is being used for visualising and pre-programming by LD’s of light-h-art. This saves valuable rehearsal time! Meanwhile in the venue the first moving head was mounted in the truss. Could also be the second one, with the two best looking colleagues who hopefully still smile after the next 1781 moving heads..
Audio has entered the building
First speaker-clusters are loaded in, working towards a total of almost 300. Sound, lights and rigging working together. Can you believe it? We are living the dream and making good progress!
Stuff, and more stuff
After the ‘official’ opening of our trailer by the ESC and Rotterdam Ahoy officials, our equipment flooded the floor: trussing, fixtures, racks and accessories. To quote a famous former ESC winner: ‘Save all your cases for me”..
Official kickoff with lots of flightcases and journalists!
The Eurovision Song Contest is a high profile production for NOS/Avrotros, for the AHOY Venue, for the producers, for artists and for technical suppliers like us, in good hands with Head of production Erwin Rintjema. The load-in is extensively covered by national press!
Points marked, trusses locked on
Precision and safety are key. Lifting points are being made exactly as designed, and the first trusses have been connected. It is all coming up to speed and getting ready for the load-in of the major part of our lighting and audio equipment and other technical stuff. Count the hoists!
The first points are for the riggers
A clean floor, a calculator, laser equipment and experience: our riggers marked the points and attached the first of many chainhoists. Being the first to go in and the last to go out, our riggers will see more of the venue than anyone else!
Meanwhile in our warehouse
Various racks are being prepared, programmed and prepared for driving the lighting systems.
Our home for 7 weeks
Our crew has entered the building, and the first ones to do that are our riggers. Their playground is an empty hall that will be transformed into a visual wonderland, for a big part hanging in the grid we supply, consisting over more than 500 chainhoststs, 2,5 KM of trussing and carrying almost 200 tons of load.
Prepping in the warehouse
Our team is preparing trusses and equipment. A big part of equipment comes from our own warehouse, but also our sister company Purple Group adds to the ESC inventory. Trusses come from Rigging Box.
Preparations have started!
After ESC2020 had to be postponed due to COVID, the game is now on for 2021. Once again we will have the honour of supplying lighting, audio and rigging for the live event in AHOY Rotterdam, as well as other festivities taking place all over the Netherlands. We are now finalising all production requests and will publish final plans when they are ready. In the next phase we will work on requests of various delegations for extra lighting and audio for their performance. We will keep you posted!